Another major delay for new Metro trains as misery mounts for passengers
and live on Freeview channel 276
The Tyne and Wear Metro’s new trains have been hit with yet another major blow, as questions continue to surround the delayed introduction of the £362million fleet.
Passengers have been warned that they will have to wait even longer for the new trains to come into service, after problems emerged that mean that the Swiss-built carriages are now in need of more rigorous testing.
Advertisement
Hide AdAdvertisement
Hide AdThe announcement marks the latest setback in a project described as the “biggest and most important” in the Metro’s history.
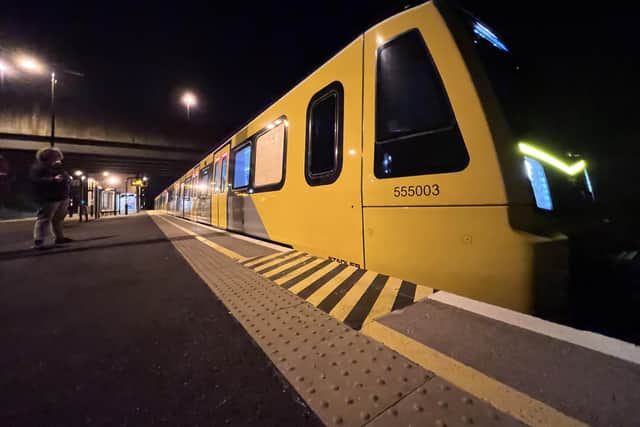

It was originally hoped that the 46 new trains, which should be far more reliable and boast modern features such as air conditioning, would be gradually introduced between summer 2023 and early 2025.
Nexus bosses later pledged that the first of the new fleet would be in use by the end of 2023, before that target date was pushed back to “early 2024” last September.
But transport officials now say that their delivery will have to be delayed even further – and are now merely hoping to have a first new train in use by the end of 2024.
Advertisement
Hide AdAdvertisement
Hide AdThe news will come as a major disappointment to Metro customers, who recently had to endure the worst period of under-performance in the network’s history.
Michael Richardson, head of fleet and depot replacement at Nexus, said that the new trains’ traction needed more testing under adverse weather conditions.
Previous delays had been blamed on the first new train arriving in the North East for local testing and driver training later than planned, as well as wider factors including inflation and the war in Ukraine.
Mr Richardson confirmed: “Before entering customer service, around 22,000 standards and clauses must be complied with, 90,000 individual tests completed and 480 of our people given extensive training. All of this is to ensure that the new trains work safely and seamlessly with Metro’s 60 stations and 77km of track.
Advertisement
Hide AdAdvertisement
Hide Ad“We’ve recently identified that further tests need to be conducted on the traction of the train, specifically when the rail conditions are unexpectedly poor. Stadler and Nexus are currently working through these now to ensure that trains perform to a high standard for the benefit of passengers.
“This is quite typical during the roll out of a new bespoke fleet and Stadler and Nexus are working closely to minimise delays to the project timescales as much as possible. We are still aiming to have the first train in service for customers in 2024 and we will have more of an exact timescale once this work is completed.”
It is almost a year since the first of the Stadler-built fleet made the journey from the manufacturer Switzerland factory to the Metro depot in Gosforth.
But there remains no sign of a new train actually being put into use, adding to the frustration felt by commuters fed up with regular delays and cancellations.
Advertisement
Hide AdAdvertisement
Hide AdThe Metro’s existing trains have been in use since the system opened in 1980 and are well beyond their 30-year lifespan, with Nexus and Stadler struggling to find spare parts to keep the ageing carriages operational.
That unreliability was a major factor in a recent dip in performance that saw a record low of just 61% of Metro trains arrive on time during a four-week period in November and December, though punctuality has since improved.
Nexus said :“We remain focused on getting the best possible performance from our current trains: Metro customer numbers have grown 13.5% in the last year and are close to returning to pre-pandemic levels. With this in mind, and the onset of Tyne Bridge refurbishment, we know Metro needs to provide a reliable service.
“Stadler is working closely with suppliers to source spare parts for the ageing fleet and we have invested further in maintenance of the current trains, bringing in heaters adapted from the airline industry to protect them through the winter. This has helped improve fleet availability – the main cause of delay – since Christmas.
Advertisement
Hide AdAdvertisement
Hide Ad“Construction of the new Gosforth depot is now complete with Stadler now having more sidings in use to better maintain, marshal and present trains each morning.
“We have also carefully reviewed our timetables to reflect current performance and improve punctuality as much as we can. Research tells us that customers value a frequent service, so we are looking to prioritise frequency over punctuality, aiming to offer customers a regular service, even if trains are not running to timetable.
“It is a challenging time and unfortunately our customers will experience busier trains and occasional longer wait times, especially at peak times. We will be advising customers to check in advance and plan ahead, allowing a little more time to complete their journeys.
“The bespoke new trains are designed and shaped by customer feedback and, when introduced, will transform the customer experience in terms of comfort, quality and reliability as well as setting high standards of accessibility. We thank everyone for their support, patience and understanding.”