Sunderland Nissan plant to produce up to 100,000 personal protective equipment (PPE) visors per week for NHS workers - next door to Nightingale Hospital
and live on Freeview channel 276
The car-maker has set up a parts processing line at the factory – next door to the planned 460-bed North East Nightingale Hospital – to help supply health staff with the personal protective equipment (PPE) they need to combat the virus.
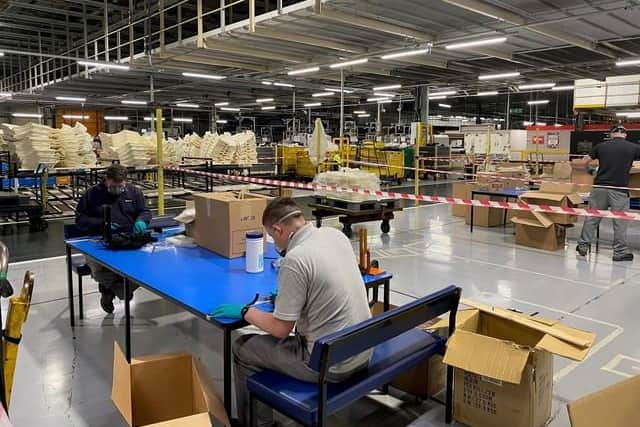

Advertisement
Hide AdAdvertisement
Hide AdThe new initiative was inspired by the efforts of four brothers, two of whom work for the Japanese manufacturing giant, who started making face guards from home with their own 3D printers.
Anthony Grilli said: “We had the ability to support the national effort to produce more PPE for frontline health workers and we just had to help.
“We quickly mobilised to produce parts using our 3D printing capability at home and we’re grateful to everyone that donated through our crowd funding site to help us get this going.”
Anthony, who works with his brother Chris at the firm’s Technical Centre, in Cranfield, Bedfordshire, initially got their home operation off the ground with the help of crowdfunding.
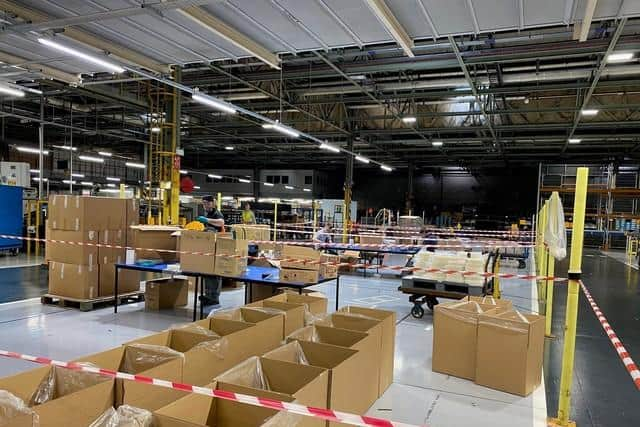

Advertisement
Hide AdAdvertisement
Hide AdBut since then Nissan has handed over extra cash for an injection moulding tool to increase the number of parts produced.
A team of volunteers in Sunderland have now created a processing line in the final assembly area at the Washington plant to sort thousands of individual visor parts and pack them in sets of 125.
This is expected to see more than 77,000 visors leave Wearside by the end of this week, rising to 100,000 from next week.
From there they will head to an NHS procurement centre and then sent on to wherever they are needed most.
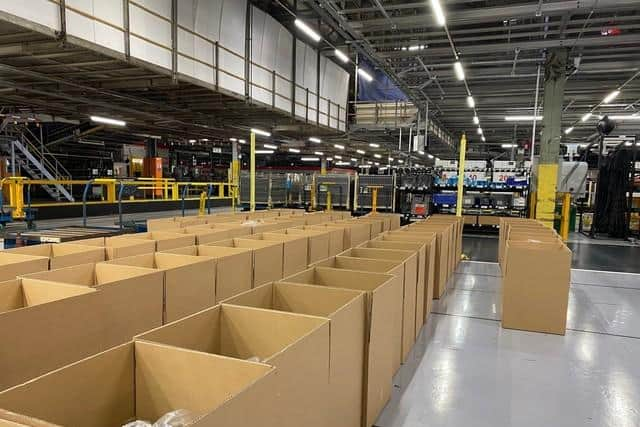

Advertisement
Hide AdAdvertisement
Hide AdBoxes of visor parts are also being sent in from volunteers from across the country who have been using their own 3D printers to make PPE.
Adam Pennick, Nissan’s production director said: “It’s great to be able to play our part in helping to provide the NHS with these visors.
“Our people are experts in the logistics behind an effective supply chain, and we certainly weren’t short of volunteers for this project.”
The process in a nutshell:
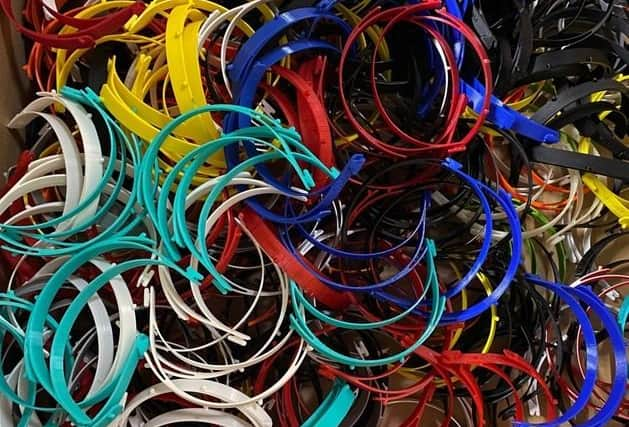

The visors are made up of three individual parts: an elastic headband, frame, and see-through visor. These parts are sent to Nissan for packing and distribution in a ready-to-assemble format to an NHS procurement centre. The visors are shipped in this format at the request of the NHS to minimise damage risk during transit, and to ensure the maximum volume can be dispatched at once.
A message from the Editor:
Advertisement
Hide AdAdvertisement
Hide AdThank you for reading this story on our website. While I have your attention, I also have an important request to make of you.
In order for us to continue to provide high quality and trusted local news on this free-to-read site, I am asking you to also please purchase a copy of our newspaper.
Our journalists are highly trained and our content is independently regulated by IPSO to some of the most rigorous standards in the world. But being your eyes and ears comes at a price. So we need your support more than ever to buy our newspapers during this crisis.
With the coronavirus lockdown having a major impact on many of our local valued advertisers - and consequently the advertising that we receive - we are more reliant than ever on you helping us to provide you with news and information by buying a copy of our newspaper.
Thank you
How to subscribe to the print edition
Advertisement
Hide AdAdvertisement
Hide AdIt’s easy to subscribe to your local newspaper. We have arranged a special 20 per cent off subscription offer for people to take advantage of. Visit www.localsubsplus.co.uk, choose the newspaper title, the type of subscription and enter your details.
Comment Guidelines
National World encourages reader discussion on our stories. User feedback, insights and back-and-forth exchanges add a rich layer of context to reporting. Please review our Community Guidelines before commenting.